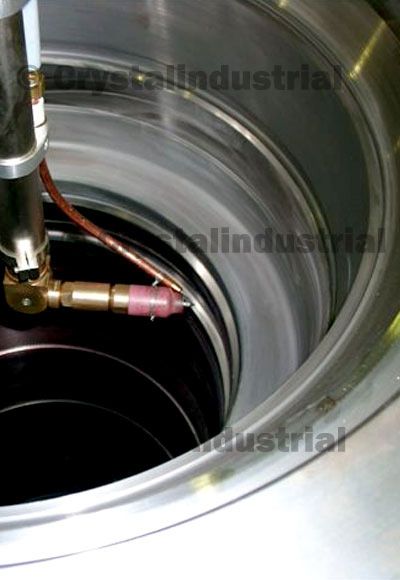
Recent Cladded Vessels Projects
Some cladding projects we have done for clients
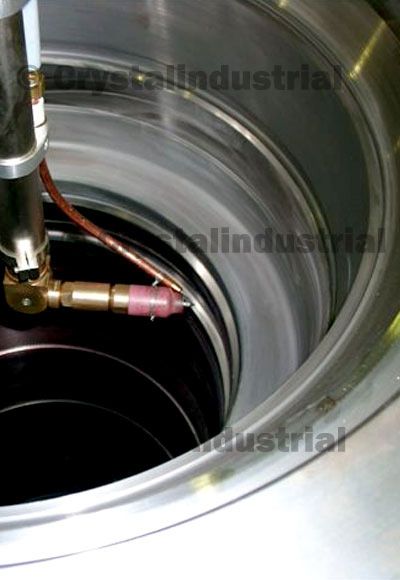
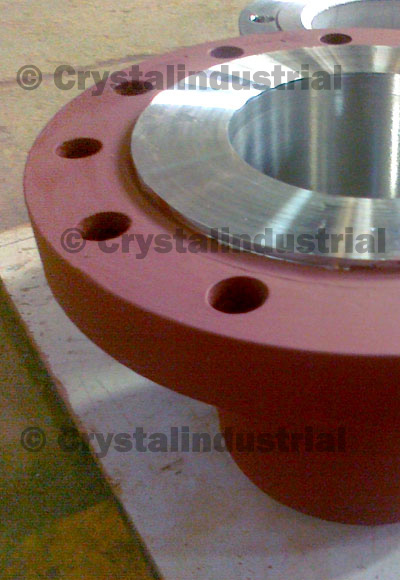
Flange Cladding
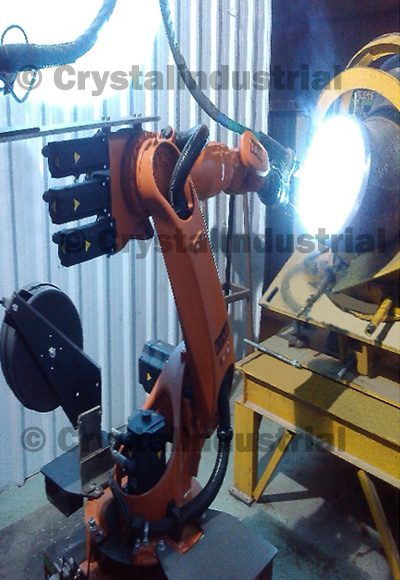
Access Fittings
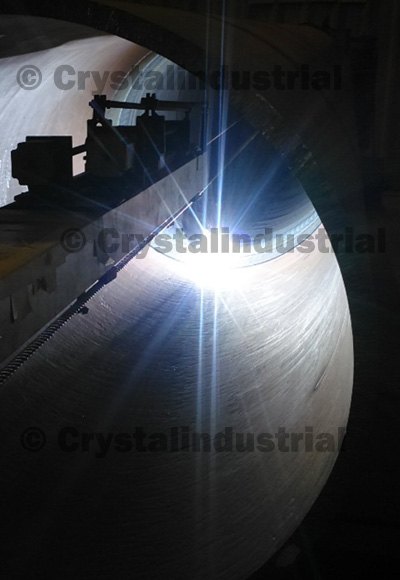
Pipe Cladding
Custom-built Cladded Vessels from India
It often happens that the material used to resist corrosion from environmental factors of a particular application may not have sufficient structural strength. Or maybe, due to its low strength it may need the use of thicker sections that are not cost-effective. A cost-effective solution comprises applying a layer of corrosion-resistant material of appropriate thickness upon the contact surfaces of the equipment, that is made from a cost-effective and structurally robust material like carbon steel. This technique of combining two layers of dissimilar materials is termed Cladding or Lining.
While Lining is a term used in a non-generic manner and covers a variety of materials, the term Cladding is employed when the corrosion-resistant layer used is metallic and also well-bonded to the contact surface. Hence, when it comes to steel fabricated equipment like shell and tube heat exchangers, and pressure vessels, the term Cladding is generally used.
It is important to keep in mind that the structural strength is provided solely by the base material. As well as corrosion, the cladding must resist the prevailing temperature, any kind of stresses that may be present, and also any abrasion. Cladding provides an attractive cost-effective alternative by offering a comparatively thin corrosion barrier of an expensive corrosion-resistant metal or alloy, with an low-cost structurally strong base material that has the capacity to withstand all loadings.
A corrosion-resistant metal or alloy layer can be fixed to the base metal in different ways. The method of Cladding comprises joining two sheets, the base material (withstanding all loads), and the corrosion-resistant material that is welded or fused using different techniques. An alternative method is the Weld Overlay, that involves welding (automatically or manually) a corrosion-resistant metal with the base metal. In either case the end consequence is identical, an inexpensive strong base material resisting the loadings plus a thin layer of an expensive corrosion-resistant metal acting as a protective layer.
The two techniques described above can be employed separately or combined.
A useful thumb rule for considering the use of cladding is as follows. For vessels that require a thickness of 75-85 mm (or more) to withstand the operating conditions, the fabrication of the entire vessel from the corrosion-resistant alloy may turn out to be excessively costly. A layer of 3 mm of corrosion-resistant alloy clad on a steel plate of 75-85 mm could reduce the cost considerably, while offering the same level of corrosion resistance. But, cladding is not the finest technical-economical choice in every case. Fabricating cladded vessels is a complex and expensive process. In addition to this, thermal cycling usually creates difficulties at weld points of nozzles and sleeves. Moreover, at the welds where adjacent sheets are merged in clad-metal construction, cracks or corrosion can happen.
The cost-effectiveness of clad against corrosion-resistant solid base materials construction rests on the unit price of the specific material, the relative cost of its fabrication, and how complex the equipment is. There are no general guidelines for when to prefer one technique or the other, the evaluation should be done on a case to case basis.
Our Services
We offer the following services for our cladded vessels
World-class cladded vessels
We make custom-manufactured cladded vessels to meet unique requirements of your processes.
Learn MoreExtensively documented
Crystal's cladded vessels offer extensive documentation and process information.
Learn MoreCommon Questions about cladded vessels
Check out the frequently asked questions about cladded vessels answered here.
Learn MoreGlobal Support for cladded vessels
Crystal's team of engineers offer global support for our cladded vessels, anywhere in the world.
Learn More